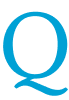
Warning letters, 483s, Recalls, Import Alerts, Audit observations
USFDA Warning letter to Dupont cites inadequate evaluation of complaints, even though the Firm received several
complaints of conductivity failure, failing to timely communicate OOS results to customers, failure to take timely actions. The site manufacture the Pharmaceutical excipient Avicel (Microcrystalline cellulose) and Warning letter follows an USFDA inspection at Delaware site during November and December 2021 and inadequate response to inspection observations by Dupont.
Failure to perform adequate investigation of complaints
Firm manufactures microcrystalline cellulose (MCC) under the brand name Avicel which is included in Drug Master File (DMF) 449 submitted to FDA. Avicel is used as a compression and flow aid in multiple drug product formulations.
Between April 2020 and June 2021, Firm received approximately 50 complaints related to Avicel excipient failing to meet the conductivity specifications. The conductivity quality standard for MCC is delineated in the U.S. Pharmacopeia (USP). Failure to meet applicable USP standards also renders drugs adulterated under section 501(b) of the FD&C Act.
Firm did not adequately evaluate these complaints. Only included retest and release data review in initial investigation into conductivity complaints for Avicel. It was not until seven months later that Firm discovered conductivity meter probe was encrusted with residue, thus giving inaccurate conductivity results. This conductivity meter was used for batch release testing and retesting as part of complaint investigations. The initial complaint investigation did not adequately evaluate whether the malfunctioning conductivity probe was potentially associated with these out of specification (OOS) conductivity complaints especially when Firm determined that the complaints could not be verified.
Firm linked this fouled conductivity meter to OOS Avicel that was previously released and shipped to customers. Firm did not communicate the OOS results to customers in a timely manner. It took more than three months after Firm opened investigation to initiate communication with customers. Appropriate action was not initiated against the affected batches until nine months after Firm became aware of the conductivity test failure.
Firm’s response letter stated, “product quality customer complaint data for the past 24 months were reviewed for trends that might indicate ineffective investigations or corrective and preventive actions,” and that “there were no significant trends observed.” This is contradictory to the customer complaint records FDA collected during the inspection. Additionally, Firm did not provide sufficient evidence of review, including a protocol, the type of complaints reviewed, how many were related to compendial test results, and Firm’s evaluation report. Firm also did not provide details on how the numerous Avicel conductivity complaints received were incorporated into the review.
Firm to provide a comprehensive, independent assessment of overall system for investigating deviations, discrepancies, complaints, OOS results, and failures. Provide a detailed action plan to remediate this system. Firms action plan should include, but not be limited to, significant improvements in investigation competencies, scope determination, root cause evaluation, corrective action and preventive action (CAPA) effectiveness, quality unit oversight, and written procedures. Address how Firm will ensure all phases of investigations are appropriately conducted.
Complaint investigations should have depth, should be comprehensive involving cross functional team members, should be timely with a sense of urgency, all the more so when the complaints are repeating.
As can be seen from the FDA warning letter manufacture of Excipients also need to comply with applicable cGMPs as per 21 CFR 210&211 and other applicable regulations just as the drug product and drug substance manufacturers.
Adequate procedure for investigation of complaints (and all types of deviations such as deviation events, Out of specification results) should be in place. The procedure should address different aspects of manufacturing and controls and product lifecycle:
Investigations should be performed by cross functional teams. Appropriate investigation tools should be used for the investigation (For e.g – Fish bone analysis, Fault tree analysis, Why-Why techniques).
The investigations should focus on identifying root cause(s) and corrective actions which will address the root cause. For example, if the cause for the conductivity failure complaints was erroneous readings from conductivity meter, this is still not the root cause. Root cause should look at why the product batches failed in conductivity parameter. If elevated levels of ammonium chloride is the reason for OOS results for conductivity in the Avicel batches, this is still not the root cause. What caused the Avicel lots to have elevated ammonium chloride. The investigations should keep asking the question till the real root cause is identified (typically this can be done through a Why-Why analysis) and CAPAs should address all the root causes identified at each stage (Laboratory analysis, manufacturing controls).
When a complaint investigation identifies the complaint as genuine, and root cause is identified, potential impact on other batches and even other products should be assessed. The scope of such assessments should cover all batches which are in distribution and live inventory. The complaint investigation should also reconcile the distribution history of complaint batch(es) as well as other impacted batches. All customers to whom the product / batches is distributed should be intimated about the lapses in the batches, whether or not they have raised a complaint. Such communications shall be timely, immediately when failure is identified. There should be procedure and system to retrieve the distribution history of each complaint / impacted batch. The investigations should be well documented. If the investigations conclude that there are no other impacted batches this should be done with sound scientific rationale.
The complaints handling procedure should also address tracking of recurring complaints. This should be a check point for complaint investigations – to check whether there were past complaints of similar nature, what corrective and preventive actions (CAPA) were implemented and whether the CAPAs were effective in addressing the root cause(s)
There should be periodic management review of complaints (as well as other Quality events and performance of the Quality Management System) and senior/ leadership management should be part of such reviews. This is best achieved by periodic Management review meetings (typically every month) with defined agenda. Minutes of such meetings should be documented and actions identified followed up and reviewed in subsequent meetings. There should be comprehensive Quality oversight in all aspects of CMC (Manufacturing controls). Procedure for Management review should be established.
There should be adequate competent personnel in the Quality (as well as other line functions) to ensure compliance to cGMP requirements. The personnel should be well trained in cGMP requirements, procedures; trainings evaluated. Training, training evaluations should be documented.
When deficiencies are identified in regulatory inspections, the observations should be comprehensively reviewed and investigated – typically a quality event (deviation) will be logged and investigations initiated. Such investigations should be comprehensive, performed against a defined protocol, scope should be well defined. The investigations should be performed with objective of identifying extent of non compliance (across batches, products, activities), root causes, impact of the non compliance and remedial actions, corrective and preventive actions (CAPA) and well documented. Such investigations and conclusions should be with sound scientific rationale, shall not contradict existing information and observations – most importantly the conclusions shall not be preconceived.
Engage competent independent cGMP expert consultant to review and assess the overall system for investigating complaints, OOS results, deviations, discrepancies and failures. The assessment should also cover all live (distributed as well as inventory) batches and products for potential failure. Based on the investigation remediation actions on impacted batches shall be taken (customer intimation, recall).
The comprehensive assessment should cover not only past complaints, but all quality events – deviations, discrepancies, OOS results, and other failures.
Appropriate CAPAs shall be identified and implemented to prevent such complaints in future. This shall address all aspects of failure – laboratory analysis, method, instrument, causes for the product failure.
Comprehensive review and enhancement of the procedures for investigation of all Quality events – complaints, OOS results, deviations, discrepancies, and failures. The procedure should address tracking the quality events, recurrence.
The independent 3rd party assessment should cover not only the systems for failure investigations, but all aspects of cGMP compliance, systems, procedures; Based on the review take up overall improvement of systems and procedures for cGMP compliance.
Actions to enhance the competency of the personnel –in cGMPs, failure investigations – hiring experienced experts, training and coaching of the personnel
Actions to enhance the Quality unit oversight as well as management oversight. Procedures should be implemented for periodic management review meeting with defined agenda which include review of Quality events and quality management system performance.
Leave a Comment
You must be logged in to post a comment.