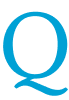
Warning letters, 483s, Recalls, Import Alerts, Audit observations
USFDA 483 to Jubilant Roorkee cited inadequate review of unexplained discrepancies, aborting dissolution testing analysis for improper peak shape though it met specified criteria, releasing the batch(es) even when unknown peaks are observed. The Jubilant Roorkee, India site (FEI 3006895982) was inspected by USFDA investigators Yvins Dezan and Rajiv Srivastava from 20 July to 1 Aug 2022 and resulted in issuance of USFDA form 483 with six observations.
Failure to thoroughly review any unexplained discrepancy and the failure of a batch or any of its components to meet any of its specifications whether or not the batch has been already distributed.
Â
Firm (on 11/10/2020) aborted an analysis for improper peak shape during dissolution test of batches of product; recorded Analytical Interruption Report No. AIR/20/0696.
Firm (on 11/10/2020) aborted an analysis for improper peak shape during dissolution test of batches of product; recorded Analytical Interruption Report No. AIR/20/0170.
Investigation identified poor column as the root cause; Based on this samples were retested in a different column and invalidated initial results. However, review of aborted sample set revealed that the peak shape for the said peak met the system suitability criteria. Review of the retest analysis sample test revealed unknown peaks eluting closely to main peak. These peaks were not seen in the method validation report 120 / HPLC Val (Effective date 12/26/2007) Validation of HPLC Method for the Dissolution (of product..).The firm shipped tablets that contain unknown peaks to US customers.
Analytical Interruption reports (industry uses different terminologies like Laboratory Error report, Laboratory Incident reports and so on) should be handled with same amount of seriousness and attention. There should be sound rationale when invalidating a sample set, analysis or chromatogram. And appropriate CAPA should be implemented so that the incident do not recur.
·       For example if a sample set is being invalidated as cited in the 483, there should be adequate elaboration and justifications – Why a sample set is being invalidated though it has met the system suitability criteria, what impact the peak shape can have on the result. The investigation should review all previous test results of the batch (covering a reasonably sufficient number of batches / time period) for peak shape performance; is it only in the specific set (which was aborted such a discrepancy is being observed. If not, there is no sufficient rationale for aborting such a chromatographic run.
·       If indeed there is a peak shape issue which could have impacted the analysis, it shows the current system suitability criteria are relaxed or not sufficiently address the requirements for proper peak shape and consistent and reproducible results. In this case appropriate corrective action should also be implemented by revising the system suitability criteria (This also will necessitate, impact review of earlier results).
Â
The 483 by FDA also show that extra peaks / unknown peaks observed in any test, including dissolution would need attention and resolution. It is not unusual to see that many times, for extra peaks in the dissolution attention is not given unless something is significantly different. The extra peaks even in the dissolution test need to be acknowledged, reviewed, concluded with scientific rationale through an Analytical interruption or incidence report before concluding on disposition of the batch(es). Firms should have several measures in place to prevent / avoid such deficiencies.
Â
Such observation will need immediate investigation as the observation raises concern on batches of drug product shipped / distributed to US customers.Â
Â
Leave a Comment
You must be logged in to post a comment.