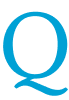
Warning letters, 483s, Recalls, Import Alerts, Audit observations
Aurobindo Unit 1 (FEI 3004021253) was inspected by USFDA investigator Rita K Kabaso from August 2-12, 2021 and issued USFDA 483 with seven observations. The 483 cited deficiencies in Change Management, and resulted in USFDA issuing a Warning letter (320-22-10 / MARCS-CMS-618091) to Aurobindo in January 2022.
Observation 1 (Warning letter)
Failure to evaluate the potential effect that changes may have on the quality of your intermediates and API.
The specification limits for an impurity in API starting material was increased. But the Firm failed to fully evaluate potential for generation of other substituted impurities. (Observation 4 in the USFDA 483). The change was implemented based on a lab scale process study (which was not part of manufacturing process) that the potential impurities will be purged out; but did not demonstrate any potential impurities will be removed. Existing related substances analytical method was relied on for detecting new impurities without determining the relative response factors and assessing the method was suitable for new impurities. In subsequent response to USFDA, Firm provided spike and purge studies data to show how the impurities are removed during manufacturing process. However response is considered incomplete by USFDA as at the time of implementation of the change in specification for API starting material, these studies were not completed. (Change Management is not effective).
The 483 also cite an instance the impact of change was not adequately evaluated while implementing a design change in an equipment.
The Warning letter asks the Firm to provide comprehensive, independent assessment of change management system – procedure, justification of change, review and approval by Quality unit, change effectiveness verification.
The key point that emerges from this Warning letter is that the process of Change handling and management is critical. The specific change cited in the 483 might not have had an impact on the impurity profile of the API; but this evaluation was performed after the implementation of the change (and USFDA citing the deficiency). The concern is that if all potential impact are not evaluated during change control or change management, it can lead to situations of real quality and safety impact on the products.
ICH Q7 clearly defines the requirement for Change impact evaluation – “Potential impact of the proposed change on quality of intermediate or API should be evaluated………………after the change has been implemented there should bean evaluation of the first batches produced or tested under the change”. (ICH Q7, Section 13).
The Change Control documentation (typically a format with a checklist), should have check points for evaluating impact on Quality, specifications, test methods, Validated status of process of the product and / or input materials, impact on Qualification status of the equipment and systems. A change of specification (Like the input material specification, relaxation of impurity limits etc) should also be subjected to a risk assessment – for e.g. an impurity in a starting material could be precursor for more than one impurity in the API (due to different side reactions, degradation). So when a revision of specification for impurity level in starting material is being proposed, the impact evaluation and assessment should consider all possible derivative impurities in API, by involving a cross functional team (CFT) of subject matter experts, R&D. Also refer to relevant information sources like the Product Development report (PDR)-Impurity controls, Drug Master File (DMF). If there is a strong rationale why other impurities cannot be formed or will be purged out (e.g due to steric hindrance, or chemical similarity of the different impurity structures ensuring effective purge out), this should be documented. Similarly a change in design of equipment / system like for e.g. change in the dimensions of a column above the reactor or change in length of stirrer, can have an impact on the qualified status of equipment and change control form should assess the same. This gives the auditors confidence about the thoroughness of change control evaluation and change management process.
The Change control form should also have check point for Change effectiveness verification; and there should be a rationale documented if a change do not require effectiveness verification (for e.g. minor changes like document templates, editorial changes etc.).
The Quality team as well as the cross functional team members who are involved in Change control request reviews should be adequately trained and informed on the impact evaluation. Case studies with live examples will help in this rather than dependence only on SOP training.
Leave a Comment
You must be logged in to post a comment.