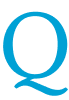
Warning letters, 483s, Recalls, Import Alerts, Audit observations
Natco Pharma (india) Kothur facility was inspected by USFDA (Investigators Pratik S. Upadhyay and Saleem A. Akhtar) in Oct 2023, and USFDA 483 issued with eight observations. Major observations in the USFDA 483 to Natco include Deficient Cleaning and Maintenance of equipment with residues on parts of equipment not cleaned since installation several years ago, coloured residue on gaskets, swab samples show residues upto 800 times acceptance level and many unidentified peaks in chromatograms, scratches and dents on equipment; Data Integrity issues with torn raw data sheets, batch record sheets, balance print outs in scrap yard, data recorded in uncontrolled white paper, tissue papers, gloves.
Other observations in the USFDA 483 of Natco include – inadequate microbial contamination control procedures of sterile products with deficiencies in aseptic facilities, airflow and visualisation (smoke studies), operator practices and gowning practices in aseptic areas, inadequate oversight of aseptic operations; Inadequate laboratory control and investigation procedures with OOS procedure not addressing R&D involvement in OOS investigations, delays in stability charging; deficient handling of alarms in manufacturing equipment and inadequate user access controls, shared user access in manufacturing equipment and no review of batch audit trail from equipment.
In this post Qvents review the Observations 1 & 2 – Deficient Cleaning and Maintenance of equipment and Data Integrity issues in the Natco USFDA 483.
Observation 1:
Deficiencies in cleaning and maintenance of non-dedicated equipment and risk of cross contamination
Observation 2:
Observation 1
Deficient cleaning, cleaning verification continue to be one of most often cited observations in regulatory audits. As discussed in multiple posts by Qvents, most manufacturing equipment have difficult to clean, not easily accessible parts. Many a time it is not so obvious / user department personnel are not aware that there can be accumulation of product dust and residues in such parts and can cause cross contamination during operation/ cleaning of the equipment. For example (but not limited to) air supply and ventilation ducts of FBE (fluidised bed equipment), Tablet coating machine, discharge lines/chutes of equipment, material transfer lines. It is critical that a Cross Functional Team (CFT) is involved during development of cleaning procedures – with personnel from Production, Engineering, QA, QC. The CFT should debate and do a risk assessment of where all product residue can carry during production / cleaning and develop cleaning procedures addressing each part of the equipment. One may need to involve the equipment supplier as well in this assessment. Equipment cleaning procedures shall elaborate the cleaning for each part, with specific cleaning verification checkpoints for each section / part of equipment. In cleaning verification and cleaning validation each of these parts shall be addressed.
Type of swab sticks to be used, stability of swab solutions, performance of a swab blank analysis (to identify the matrix peaks and avoid false alarms) are essential aspects to be addressed while defining testing procedures for cleaning samples. While establishing and validating a test procedure for cleaning sample analysis ensure at a minimum the following are addressed:
While documenting the test procedure ensure all precautions like solution stability, type of swab sticks to be used, other do’s and don’ts of the test procedure are documented. Procedurise the same into a general SOP and checklist for e.g.; Procedure for establishing and validating cleaning test procedures. It is always a prudent strategy to validate same swab stick for different products, unless it is not an option due to specific sample characteristics. This will avoid the issue of having to maintain inventory of different type of swab stick stationary. It is possible some of the test procedures where developed several years back with different swab sticks. Even in such cases it is more convenient to revalidate (with minimum set of parameters – matrix interference, swab recovery) the test procedures with more commonly used swab sticks, to avoid inadvertent mistakes at analyst level during sampling and analysis.
QC being the agency for testing of the samples (and in turn responsible for logging incidents / deviations / OOS in case of discrepancies or non-complying results), it is imperative that QC / Laboratory is aware of the cleaning / swab test limits. QC shall provide the results with comments whether the samples are complying or not to QA, who shall review the data and decide clearance of equipment for next product. In case of any discrepancies or test result not complying to limits, QC shall initiate logging of a Quality event and along with QA and other relevant functions initiate an investigation.
Condition of manufacturing equipment with severe scratches, visible dents, chipping does raise auditor concerns, especially if there is no documentation and risk assessment of such issues. This raises concerns about Firm’s equipment upkeep and maintenance procedures, cleanability of the equipment, competency and skills of personnel involved in operations. The issues causing such situations (scratches, dents etc) should be comprehensively understood and addressed – providing appropriate tools for the personnel for material discharge and cleaning; training personnel on GMP and acceptable and non-acceptable shop floor practices (for e.g. many times dents and scratches are developed due to hitting the equipment body for dislodging sticky material, scratching the material from equipment and others. And still events could occur causing dents/scratches on equipment. But rather than waiting for such issues to be picked up during regulatory audits, log the incident as a Quality event and investigate, perform impact assessment. Capture the event in the equipment history card for easy traceability of the event and its investigation during audits. Put effort to identify the root cause(s) for the events and establish CAPA – improve cleaning procedure, appropriate tools for material discharge, training. This gives the auditors the confidence that when events happen, there is a system to document, evaluate, investigate and identify solutions.
Observation 2 – Quality oversight over control of GMP documents, Data Integrity.
Recording of raw data on uncontrolled sheets, tearing of GMP records, updating of records non contemporaneously, control of GMP documents and raw data sheets are fundamental to GMP. The ICH Q7A (Section 6), USFDA Guidance on Data Integrity, EMA Guidance on GMP and Questions and Answers on Data Integrity and similar guidelines from different agencies clearly establish the tenets for control of cGMP documents and Data Integrity – Parent procedures for all cGMP documents, Identification and Traceability, Authenticity, Version & Revision control, Retention, control of disposal of cGMP documents.
Still one of the most often cited deficiency in audits is on document control and data integrity – shows how important it is for Companies to establish and nurture a quality culture based on the pillars of integrity, compliance, transparency, accountability.
It is fundamental that Companies establish robust procedures for control of documents and data in line with regulatory requirements which is straight forward and not so complex.
Qvents has discussed the regulatory requirements for Document and data control and Data Integrity and actions companies should take in several posts; To cite a few:
Apart from establishing robust systems and procedures for document controls, there should be a strong focus and efforts on establishing a Quality culture and nurturing and sustaining it. This shall be driven by the top management with right messaging, leadership by example, involvement in shop floor activities and engaging with employees, Gemba walks, regular reviews. A culture of Quality, Compliance and Integrity should be sustained through continuous measures:
A McKinsey presentation Building Quality Culture and Capabilities in an IPA conference 2019 highlights five pillars of Quality culture Quality as top priority, Open dialogue (transparency), Employee Ownership, Leadership (Lead by example), True resolution of problems which very much resonate with the points discussed above.
The true resolution of issues when Quality events happen (Deviations, failures, discrepancies) is a critical element of Quality culture as well as Integrity. Inculcate a culture when deviations / failures happen, they are investigated in sufficient detail with adequate time, root cause is established and CAPAs identified before the issue is concluded and closed. Empower the team members and the Quality unit to take appropriate decisions so that issues are resolved rather than events are just managed.
Training as a CAPA for Quality events can only be part of the actions. The focus in investigation shall be the primary event, what caused the event and what are corrective action for the same. (For e.g. what caused the pages to go missing in a BMR; was it that no proper storage space in operational areas for issued documents, uncontrolled access to documents; or personnel removed the pages for hiding some activity gone wrong). And when training is identified as one of the CAPA, the process of training assessment shall be scientifically sound. If training assessment is performed through an interview with employee, summary of the interview shall be documented. If a questionnaire-based assessment is performed, ensure the questions are relevant to the event, rather than picking up some related questionnaire.
Leave a Comment
You must be logged in to post a comment.