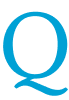
Warning letters, 483s, Recalls, Import Alerts, Audit observations
USFDA 483 to Sunpharma, Mohali unit in Aug 2022 cites Data integrity issues and Backdating, records of activities performed by personnel and personal entry /exits record do not match, deficient investigations. Further the site was put under OAI category and in April 2023 USFDA issued a Consent Decree /Non compliance letter restricting release of batches to U.S from the Mohali site
Observation 1.
Failure to thoroughly review any unexplained discrepancy, whether or not the batch has been already distributed.
Observation 2.
Established sampling plans, test procedures and laboratory control mechanisms are not documented at the time of performance.
1. Building access records showed an employee responsible for collecting samples did not enter the building where the samples were documented to have been collected, or that employee was in a different building at the time the samples was documented to have been collected.
a. Samples were documented as having been collected by an employee from production block; but the building access records show the employee accessed the Documentation cell in a different building (using badge access cards); the badge access cards show no entrance or exit from Production block. In another instance badge access records show employee in production service floor while sampling records show samples collection from another block & building at the same time.
b. Badge access records show an employee leaving microbiology laboratory at 11.03, while sampling documentation show sampling performed at 11.03 in service floor of production block. The badge access records show no entry, exit of employee from service floor. (Other similar incidents are observed)
c. In another instance, sample records show sampling performed in manufacturing area in the production block at 12:37 by an employee, but badge access records show the employee was entering the Quality Dining Room at 12:35, in a different building. (Other similar instances are observed – Observations d,e,f)
2. Entries were not made into GMP records contemporaneously.
a. On August 3, 2022 Logbook for incubator did not have an end of incubation date, time and signature for samples collected on July 27th, 2022 and withdrawn and read on August 1, 2022. (Other similar observations)
This is tough, laborious, time consuming; but there is no easier way. Which is why prevention is better than cure.
FDA has published the Consent Decree letter issued to Sunpharma. Access the same @ https://www.fda.gov/media/167956/download. In the letter FDA has mentioned that “On March 13, 2017, FDA authorized Sun to resume drug manufacturing operations at the Mohali facility; however, the Mohali facility remains a Covered Facility under the Decree”. However, based on the August 2022 inspection FDA has determined that, the facility is not compliant with applicable regulations and the Decree. FDA has ORDERED Sun Pharma to take corrective actions before any batches are released for distribution in U.S. Sun Pharma should appoint an independent cGMP expert who should submit to FDA a written batch certification protocol which should be approved by FDA. The cGMP expert shall witness manufacture and testing of all drugs, provide a written certification for each batch signed by cGMP expert as well as responsible Sun Pharma employee. This should be submitted to FDA prior to releasing each batch.
Log in to Reply
Leave a Comment
You must be logged in to post a comment.