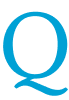
Warning letters, 483s, Recalls, Import Alerts, Audit observations
USFDA Warning letter to Centrient India (Toansa, Punjab FEI 3004497364) in December 2022 cited inadequate document control over paper and electronic records, uncontrolled document shredder with unidentified shredded documents, multiple usernames and passwords for software logins for several users handwritten in a note book. Warning letter followed USFDA inspection at Centrient India site in June-July
2022.
Failure to ensure adequate document control over paper and electronic
records. Observed numerous logbooks, forms, and partially completed “Sample
Request For Analysis in an uncontrolled temporary storage room. In the document center observed
a document shredder labelled for “emergency use” containing
shredded documents. Unable to identify the documents in
the shredder that were observed to contain information for relative humidity,
temperature, and data recorded in writing.
Failure to
have adequate controls for your computerized systems. Multiple
usernames and passwords for software login of several users’ information were
handwritten in an uncontrolled notebook of senior executive
microbiologist. The login information was for software used to control laboratory
equipment, such as incubators for the storage of product and water samples. To
ensure data integrity, actions performed need to be attributable to a
specific individual.
Response
does not provide a detailed plan to ensure future paper and electronic
record and documentation practices comply with CGMP. Response is also
inadequate because it does not include a comprehensive retrospective
risk assessment of the impact and scope for the inadequate document control at
the facility, and it does not fully address tiered user access and controls to
ensure access is appropriate to each users’ role and administrative roles are
adequately controlled.
Inadequacy of absence of policies, procedures with respect to data integrity, document control – issuance, maintenance, retrieval, archival, destruction of paper documents or their implementation lead to such observations during regulatory audits. Companies in a GxP domain should have procedures and practices for control of computerized systems and electronic data – defined and controlled user access levels; password policy & controls; data archival, retrieval, audit trails; computer system qualifications and validation (CSV).
Companies should have robust document control procedures for paper documents and implementation of the procedures and practices covering document issuance, maintenance, review, retrieval, archival and destruction. There should be accountability of all documents through issuance and retrieval logs; Quality unit (Quality Assurance department) should be the custodian of the same. Document destruction should be a controlled activity with authorization from Quality unit and logs maintained. Document shredding machines (shredders) should also be controlled with logbook and documentation of shredding activities performed. Document archival and storage locations should be well defined with access controls.
There should be policy, procedures for control of computerized systems. Administrative controls should be defined and should be with independent units (usually the IT function reporting to top management). Computerized systems should be 21 CFR Part 11 and electronic data control requirements compliant. This will include – defined procedures for password controls [individual passwords for all named users, defined expiry of passwords (usually 1 month), password complexity (minimum length and requirement of combination of letters, numbers, symbols), non repetition of passwords (eg: a password should not be same as at least last 3 passwords), password reset by users (without any need to write down passwords)], defined access privileges for users which is consistent with user roles in all systems, procedures for activation and deactivation of users and user privileges, There should be procedures for control of electronic data – data archival, retrieval, review of audit trails. If there are certain legacy computerized systems where some or several features of 21CFR Part 11 compliance are missing, an assessment should be performed with respect to risk to data security, data traceability. Accordingly remedial measures – alternate controls or replacement of systems should be taken up. There shall be no uncontrolled usage of passwords, sharing of passwords. Defined procedure for Computer systems qualification and validation (CSV) and all GxP computer systems should be qualified and validated.
Companies should have well defined data integrity policy, which include policies for control of computerised systems and electronic data compliance. All employees of the company should be well trained in the policies and procedures. There should be active oversight and control of Quality Management system performance and Data Integrity by Quality unit & periodic review by top management. (e.g. monthly management review meetings. Such review should cover review of data integrity incidents and actions taken, apart from review of Quality events & trends such as complaints, deviations, out of specifications and out of trends. There shall be defined procedure for management review meetings with agenda, presentation templates, documentation of minutes and action points.
Leave a Comment
You must be logged in to post a comment.