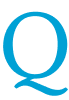
The Warning letter cite Failure of Quality unit in ensuring cGMP compliance, Inadequate control over paper and electronic records – blank analytical worksheets and other cGMP documents, multiple cGMP documents with same control number, shredding of cGMP documents after terming them as “discard waste papers”; Failure to appropriately test materials; Inadequate cleaning of equipment with material encrusted and peeling off from “Cleaned” equipment. The June 2023 Warning letter was issued to Centaur after USFDA inspection observed significant deviations at the API facility at Ambernath near Mumbai (FEI 3003973520 ) in November 2022 and inadequate response by Centaur.
1. Failure of Quality unit to exercise its responsibility in ensuring cGMP compliance
A. Inadequate document control over paper and electronic records
B. Quality Unit failure to ensure that materials are appropriately tested and result reported
Firm’s response (to deviations) is inadequate as it has not identified the scope and extent of its practices of discarding and shredding cGMP documents, issue of multiple documents with same document number, unlabelled vials in HPLC and the Firms cGMP training programme is inadequate.
Firm is asked to perform a comprehensive assessment and review of documentation system throughout the manufacturing and laboratory operations, material system (qualification, analysis, release), laboratory practices and analyst competencies, training programme effectiveness for QC and laboratory operations, provide a remediation plan which ensure adequate resources and authority to Quality Unit.
Observation 2:
Failure to clean equipment and utensils to prevent contamination and carry over:
Firm is asked to perform comprehensive, independent, retrospective assessment of cleaning effectiveness, cleaning program.
1. Document control, laboratory control and labelling of samples
Control of cGMP documents – issuance, retrieval, reconciliation, archival and retention and retirement (destruction after completion of retention period) is of paramount importance. It will not be an overstatement to say the reliability and integrity of the Quality system and Firm is as good as its document control system. When there are uncontrolled blank forms, analytical worksheets, other cGMP document in a site, it directly cast doubts on integrity of all activities performed – manufacturing process and controls of batches, handling of quality events, analytical reports, training records so on and so forth. Various citing of finding GMP documents in scrap / shredded documents during audits, reinforce the point that if an auditor picks up such a piece of document from anywhere in the site and challenge the document control and integrity, Quality unit and the Firm should be able to trace and explain the shredded / scrapped piece of document and why it was scrapped. There should be strong internal review and checks to identify any violations. Observation of multiple documents with same version number, shredding of documents without traceability are clear pointers. Executive Management and leadership should ensure appropriate Quality culture and oversight over operations and compliance and adequate resources and authority to Quality Unit to ensure compliance.
2. Failure to clean equipment
Almost all manufacturing equipment have difficult to clean, difficult to reach areas for cleaning (material transfer and discharge lines and ports, chutes, air supply ducts and ventilation ducts in equipment like Fluidised Bed Driers, Multimill blades and so on). Equipment cleaning procedures shall be developed by discussion within a cross functional team (CFT) involving Manufacturing, Engineering, QA, QC and even Equipment vendor, to understand all product contact parts and possible areas where product residue accumulation can happen. Product change over cleaning may require complete dismantling of equipment for reaching all hard to clean areas. Cleaning procedure /Cleaning verification checklist should detail every component and contact surface. Perform a risk assessment of potential cross contamination from each equipment by the CFT, identify all potential areas where product dust/residue can reach, address the same in cleaning procedure and cleaning verification. Inputs from Engineering department will be critical to identify all areas product residue / dust can travel during manufacturing and cleaning operation. Accordingly develop/ enhance cleaning procedures and cleaning verification checklists.
Cleaning, Cleaning verification and Cleaning validation is of highest concern with non dedicated equipment and accessories. The CFT can also review where the equipment cleaning and assurance of cleanliness is most difficult and scope for dedication of such equipment, accessories for specific products (For e.g. Sifter screens, Discharge chutes in Equipment like Sifters, ANFD). A control procedure with verification checks also need to be established to ensure these dedicated equipment / accessories are used only for the specific products. This can also help ease out the rigour of cleaning / verification requirements and significantly reduce product change over times.
Establish Cleaning / Cleaning verification and Cleaning validation programmes considering worst cases – product with highest toxicities / potency, most difficult to clean, lowest solubility. Establish the Maximum carry over limits (MACO) for each product. Cleaning procedure adopted shall be able to clean the drugs with highest toxicity / potency and most difficult to clean to below the allowable limits for carry over into the next worst case product (typically smallest batch of the next product. Establish appropriate sampling procedures (rinse and swab sampling) from worst case sampling locations -hard to clean, hard to reach in each equipment, identify the same with equipment drawings and document the rationale. (Refer the APIC guidelines for Cleaning Validation & other guidelines on Cleaning Validation by EMA, WHO, USFDA).
Establish maximum hold times for equipment before cleaning (dirty hold time); As a practice ensure cleaning as soon as possible after a batch operation is completed in an equipment. More time equipment are left unclean, more difficult it is to clean, degradants develop which may not get detected in the cleaning sample analysis.
1. Document control, laboratory control and labelling of samples
Lack of control of cGMP documents touches the core of compliance and integrity. When Firms find issues in this area (through internal or external audits) the remediation approach should be holistic and comprehensive.
2. Failure to clean equipment:
Peeling residues, encrusted material on equipment and accessories which are with a status “Cleaned” raise serious contamination / cross contamination concerns and straight away raise a cause for Product recall. When Firms face such situations, a comprehensive, in-depth systematic evaluation of the contamination issue and risk assessment can help limit the batches to be recalled to those most at risk. For e.g.
Leave a Comment
You must be logged in to post a comment.